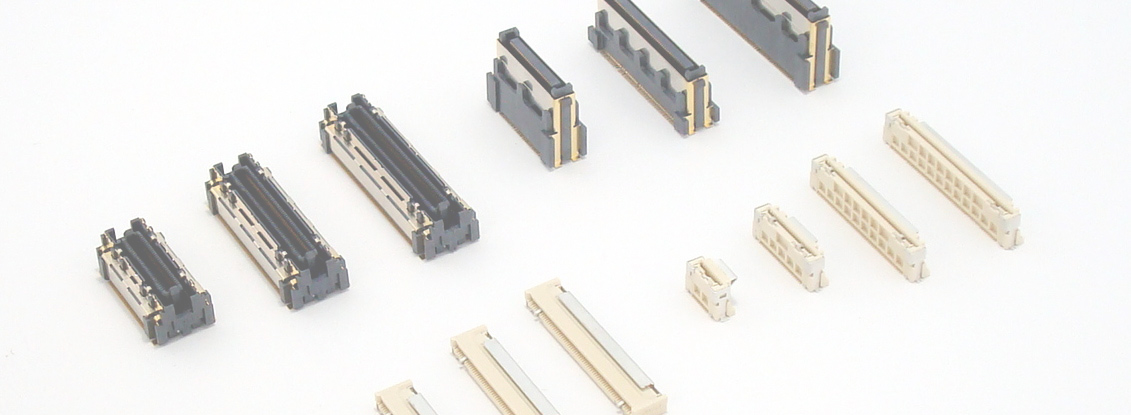
When it was necessary to seal a mounting board with resin, this was conventionally done using a method called "hot melt," in which thermosetting resin or low-melting-point thermoplastic resin is molded at relatively low pressure.
On the other hand, highly heat-resistant thermoplastic resins, such as engineering plastics (ENPRA) and super engineering plastics (SUPER ENPRA), have not been put to practical use due to concerns about damage to components and their soldering parts caused by the heat and resin pressure that occurs during resin molding.
However, if it were possible to directly mold a circuit board on which components were mounted using engineering plastics or super engineering plastics, various possibilities for packaging were conceivable.
We will also be able to utilize the know-how and production technology we have cultivated in our connector manufacturing.
Therefore, we have worked to establish and perfected high heat-resistant thermoplastic resin insert molding technology.
We will also be able to utilize the know-how and production technology we have cultivated in our connector manufacturing.
Therefore, we have worked to establish and perfected high heat-resistant thermoplastic resin insert molding technology.
Problem solved: Damage caused by heat and pressure during molding
Advantages: Achieving both productivity equivalent to that of connector parts, dimensional accuracy, and reflow heat resistance
The newly developed technology has made it possible to insert mold using resins known as super engineering plastics, such as LCP and PPS. Compared to conventional methods, this technology has broader applicability in terms of processability and post-packaging parts, making it suitable for a variety of uses.
Thermosetting Resin | Hot Melt | New Methods | |
---|---|---|---|
Reflow correspondence |
◎ Thermosetting resin is OK |
× Not durable due to low melting point material |
○ Uses proven high heat resistant resin |
Productivity cost |
×~△ Resin is expensive Cure process required Not suitable for mass production |
◎ Relatively inexpensive resin |
◎ A proven connector manufacturer Resins and Processes |
Formability Dimensional Accuracy |
△ The method of forming the shape is complicated Problems with shrinkage and burrs during curing |
× Contains a lot of soft wood and is not suitable for product exteriors Poor dimensional accuracy |
◎ Proven track record in connector manufacturing |
This technology has a wide range of applications, including reflow mounting of package components, packaging with integrated IF mechanisms, and waterproof products. We plan to consider various additional resins depending on the application.
We are currently seeking opportunities to apply this technology, so if you are interested, please feel free to contact us.