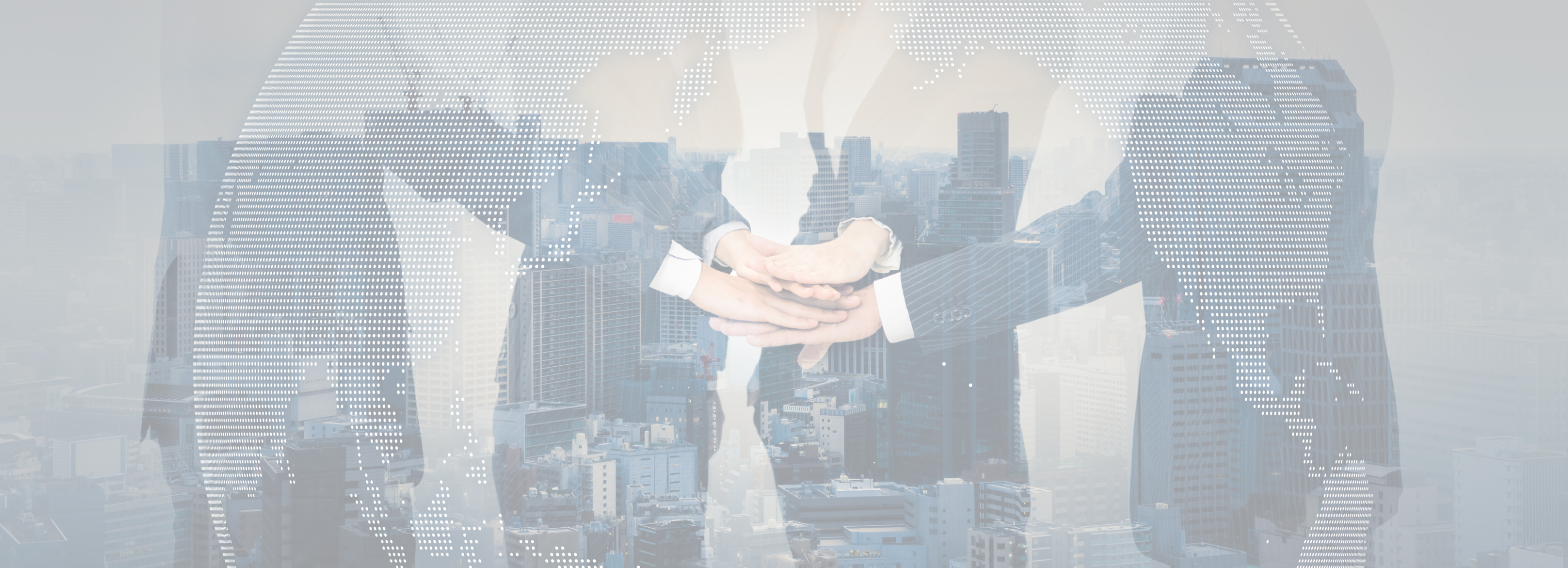
At IRISO, we diagnose the connection status between boards in your equipment under the expected vibration environment and provide a full range of support, from proposing optimal products. We would like to introduce our unique vibration analysis simulation, which we can provide precisely because we have been involved in the development of connectors for in-vehicle equipment for many years.
As everything becomes electronic, including electrical drive, control, management, and calculation, the environments in which electronic components are installed are becoming more and more diverse.
Some of these products are exposed to severe vibrations, so there are many CAE tools for vibration analysis that are designed for use in such environments. Most of these tools simulate the resonance frequency, acceleration, and shock that occur in components and their mounting parts due to vibration, as well as their resistance to these vibrations, making them extremely effective tools for assessing the risk of component failure in advance.
IRISO manufactures and sells Board to Board Connectors for vehicles that are used in extremely harsh vibration environments. These products are commercialized after undergoing reliability tests such as vibration tests, but to provide optimal proposals for incorporating them into actual customer products, it is necessary to understand the behavior of the actual equipment.
For connectors that connect boards, in addition to resistance to acceleration and shock, it is also important to consider how Mating Height changes under vibration. For example, if the relative displacement between boards changes due to vibration, the connector itself will also change, and concerns will arise as to whether each mechanism can follow the displacement or whether micro-friction wear of the contacts will occur.
However, there were no CAE tools on the market that could check these things in advance.
Therefore, IRISO has developed its own analysis tool that allows us to assess the risks in advance by having customers disclose information about mounted components other than the board and connector, and even to propose design changes such as optimal connector design and board layout according to the situation.
Conventional main vibration analysis methods | Developed vibration analysis method | |
---|---|---|
Key parameters | Frequency, acceleration, displacement | Frequency, acceleration, Displacement + Phase of Object |
Impact on components mounted on the board | 〇 | 〇 |
Impact on board-to-board components | × | 〇 |
It is said that approximately 80% of mechanical device failures are caused by "fatigue and wear." In a vibration environment, even a small force/movement can be repeated tens of thousands or hundreds of millions of times, causing material fatigue and wear, resulting in risk of destruction. The same is true for connectors. Therefore, by performing simulations in advance, it is possible to reduce the movement and product resistance to a level that can be tolerated even if it occurs tens of thousands or hundreds of millions of times, both in terms of board design and connector selection.
IRISO 's vibration analysis simulation verifies the effects of vibration from the design stage and provides feedback to the design to avoid the following risks.
These risks can be avoided by using simulations that focus on board-to-board displacement and are specialized for connector connections. We then propose optimal products based on that analysis.
IRISO 's vibration analysis simulation uses our unique technology to calculate the relative displacement between boards in the following flow:
Based on the amount of relative displacement between the boards calculated above, we can propose the optimal connector.
We propose Z-Move structure series as a measure against micro-sliding wear when relative displacement occurs in the connector mating direction, and a less expensive connector in cases where this is not a concern.
We have a wide variety of Board to Board Connectors, so we can make proposals that meet a variety of analysis results and needs.
* Floating Connector are recommended for customers who are concerned about misalignment due to factors other than vibration, such as when using multiple connectors, or who wish to improve assembly workability.
** The Z-Move structure connector is the world's first Board to Board Connectors that has a Floating in the mating direction, intended to prevent micro-sliding wear of connector terminals in a vibration environment.
*** Depends on contact pitch and connector size.
Additionally, for areas in the diagram above that require a design review, we also offer suggestions for reviewing the board layout.
For example, we can propose measures such as changing the fixing position or method of the board to eliminate resonance points from the expected frequency range, or changing the connector position to keep the relative displacement between boards within the regulations.
By providing such consultation from the early stages of development, we can contribute to streamlining our clients' development processes and quickly identifying and resolving potential issues.
The vibration analysis introduced here is conducted as a means of support when you are considering adopting our connectors.
For details, please consult with our sales staff or contact us via this page.
In order to carry out vibration analysis, you will need to provide the following information: