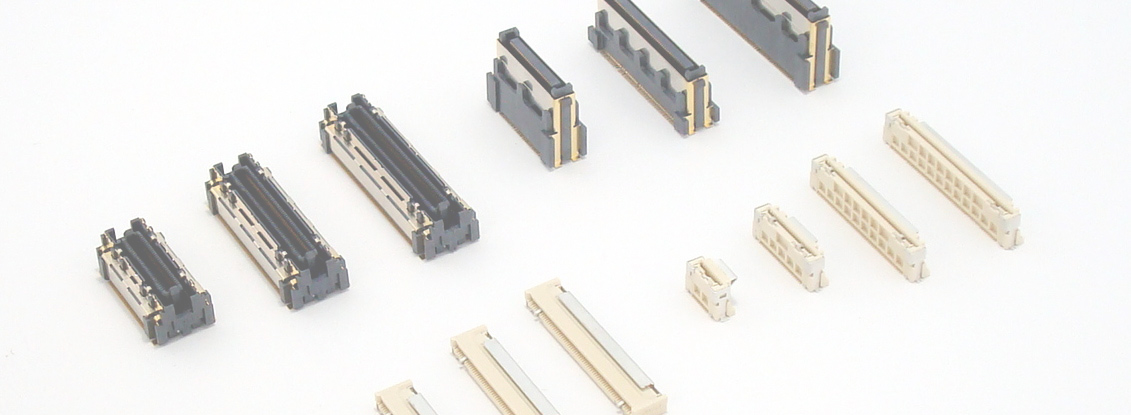
Have you heard of the alloy called Galinstan?
This alloy, which is made of gallium, indium, and tin, has an extremely low melting point of -19℃ for a metal. In other words, it is a metal that is liquid at room temperature. It is used in thermometers as a substitute for mercury, the use of which is restricted due to its toxicity, and various other applications are being researched.
At IRISO, we thought that by applying the characteristics of Galinstan to connector technology, we could create a completely new product. To date, we have been considering various concepts and continuing our research toward practical application. This time, we would like to introduce some of our research.
When considering the application of Galinstan, the most distinctive feature is, of course,
That's the point.
Their low toxicity leads to product safety, and they have the advantage of being able to be formed into any shape compared to solids.
Connectors contain metal parts with complex shapes that enable their mechanisms to function.
Furthermore, it is possible that liquids may be able to overcome the limitations on miniaturization that exist from the standpoint of processability.
On the other hand, because it is a liquid it will flow away if left as is, so finding some way to retain it becomes a challenge.
The characteristics that give hints for retention are
This feature can be utilized in commercialization.
On the other hand, when using it as a connector, there are concerns about its relationship with the following solid metals.
In order to commercialize it as a connector, it will be necessary to use solid metal and liquid metal parts according to the requirements of each part. In other words, the challenge will be to combine Galinstan with other solid metals, i.e. to match them in the form of contact.
To summarise briefly, the following possibilities and challenges become clear:
Expected benefits/possibilities |
---|
Less restricted movement ・Low stress Mating: Ultra multi-pole connector |
Not easily restricted by shape - Effective filling of complex shapes |
Can be made smaller ・For ultra-small/ultra-thin connectors |
Issues to be verified and resolved |
---|
How to retain and maintain it? Fix it |
Matching with solid metals - Maintaining healthy contacts |
Other basic connector reliability
Contact resistance |
From the perspective of miniaturization, one of the advantages mentioned in the previous section, we have conceived and are currently developing a film-type connector that is configured on an FPC as a zero-height, low-contact pressure connector.
Specifically, the project aims to create a female film by using surface tension to hold Galinstan filled in a VIA cup in place of a male film that has bumps made from solid metal, thereby achieving a connector connection similar to that of a band-aid.
We will introduce an example of pre-verification that was conducted prior to development.
The following is a copper plate that has been plated in various ways, coated with Galinstan, and left at high temperatures.
This is an overview of the confirmation carried out.
These results eliminate concerns about the evaporation of Galinstan and confirm its potential to be connected to certain metals.
After carrying out the above-mentioned verification tests, we became convinced that the concept was feasible and created an actual prototype.
A VIA cup like the one shown below was formed on the female side film that will be filled with Galinstan, and a bump was formed on the male side film.
We prototyped a mating connector using two rectangular films arranged in a 6x6 pattern with the upper structure as the contact points.
Below are some images and diagrams of the actual prototype.
It has been confirmed that the prototype connector can Mating with a contact resistance value that is sufficient for the connector to function properly.
We are also currently continuing to evaluate our environmental dependency and reliability. Below are some examples.
We are currently investigating more specific application targets. We are also looking for partners who will consider applications together with us, so if you are interested, please contact us.
Our company, which specializes in Floating Connector, also releases high current compatible products as variations of the product. A representative product is the 10122B/S series, which is compact in size but has a high current capacity of 15A.
10122 series
https://www.irisoele.com/jp/series/view/10122B/
https://www.irisoele.com/jp/series/view/10122S/
One of the key points for allowing a connector to pass a large current is to reduce Joule heat caused by resistance loss, in other words, to reduce resistance at each part of the current path.
The 10122B/B series is a high heat resistant (125℃ rated) connector that achieves low resistance without interfering with Floating structure movement by branching Floating part, and also improves reliability with a four-point contact structure. It has been evaluated as an attractive option for power transmission in board-to-board connections that require Floating, and has been adopted by many customers.
Not satisfied with the current situation, we are considering ways to handle even higher currents.
However, even in the 10122B/S series, which has this ingenious spring structure, Floating spring is the largest heat source when a high current is applied. In Floating Connector, which is characterized by absorbing misalignment, improving assembly, and relieving stress in the board mounting area, the spring strength of Floating part cannot be made extremely strong.
This requires that the spring section be narrowed or tapered, or that it be routed long, which inevitably results in a certain degree of high electrical resistance.
We are currently working on various ideas for the terminal structure design to achieve both high current compatibility and Floating, but at the same time, we considered whether there was a way to make a breakthrough from a completely different approach.
Then, I had the idea that Galinstan, which I had been researching, could be applied to this issue.
Therefore, we considered a structure based on the 10122B/S terminal, which could be separated into two pieces, had a bold Floating spring, and reconnected with a joint part filled with and sealed with liquid metal. We actually built a prototype and carried out evaluations.
After creating and evaluating samples, the first prototype, which used the 10122 terminals, was able to reduce the amount of heat generated by nearly 40% when a high current was passed through it.
As a next step, we are completing the design of the terminal structure that will make the liquid metal terminal joint more effective.
Preliminary simulation results show that the amount of heat generated is expected to be reduced by 65% compared to current products.
Our findings to date have confirmed the significant benefits of applying liquid metal to high current Floating Connector. There is still a long way to go before we can commercialize the product, from optimizing the design to building the production process and optimizing costs. We will continue to develop the product further, aiming to be of service to our customers.
At IRISO, we welcome your requests regarding other applications of liquid metals. We also welcome joint development projects.