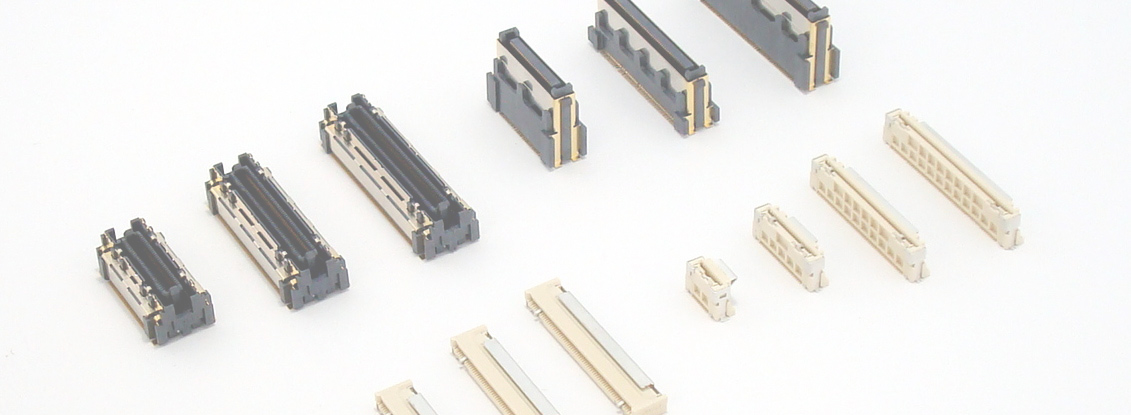
If you search the web for "High heat-resistant Connector," you'll find a variety of products, ranging from those with a heat resistance of about 80°C to those that are said to support up to 680°C. It can be a little confusing for some. This time, I would like to talk about "What is a High heat-resistant Connector?" In the ambiguous definition of the word, I would like to explain what constitutes high heat resistance, including applications, technical issues and approaches, and special cases.
This is not limited to connectors, but in addition to high heat resistance, the definition of height is rather ambiguous for products with "high" such as high-speed transmission and high current. If there is a difference in recognition between the sender and the receiver of the words, there are times when the conversation does not mesh well. Even in our sales activities, if we do not fully understand the customer's needs, we may end up making irrelevant proposals, so each salesperson pays attention to initial communication... However, even if misunderstandings are quickly resolved, there still seem to be occasional misunderstandings.
Case ①
Case ②
Examples of misunderstandings due to the interpretation of “high”
The reason why such a misunderstanding occurs is that what is expensive differs depending on each market, product, and environment. For example, even with the same product, if we bring our high heat resistance and high speed transmission products to the automotive market and the communication equipment market, the reception will be different. etc. is received differently. Occurs because ``higher than'' rather than absolute height ``high'' is associated with ``high crown'', such as ``more than xxx'' or ``for xxx'' It's a misunderstanding.
For example, in the case of medical diagnostics such as blood pressure, there are clear medical standards, and "high blood pressure starts here". On the other hand, if someone with a height of 178 cm were in Japan, they would probably say that he is reasonably tall. However, if you go to Holland, it doesn't seem strange to be told that you are short. Or even if you go to the baseball world and say, "A straight ball with an angle that comes out from a tall person of 178 cm!"
Handling height changes in the environment
As explained in the "What is a connector?" section of the Technical Info on this site, the diversification of uses for connectors has led to similar problems with high heat resistance. Therefore, if you remove the premise, a simple web search at the beginning will result in a confusing lineup of this and that at the same time. It may be troublesome for those who are looking for parts that can be used for a specific purpose, but the purpose is to narrow down the search by adding keywords such as "connector high heat resistance XX connection". becomes easier to reach.
Let's look a little more specifically at the difference in meaning of "high heat resistance" depending on the type of connector. The system of materials used and the sense of size differ depending on the type of each connector. In particular, there are types with a heat resistance of 200 to several hundred degrees Celsius, such as those used for connections in heaters and heating furnaces, as well as those with a 150 degree Celsius rating even in areas where the temperature drops a little more in the vicinity. There are connectors for wire connection, etc., which are also called High heat-resistant Connector. For the former, ceramic insulators, which are not often used in other connectors, or plastics or materials such as PEEK, which are highly heat-resistant and strong among super engineering plastics, are used. The metal parts are also made of stainless steel with a solid structure.
On the other hand, connectors for general-purpose in-machine wiring are based on a 60°C rating, and those rated at 80°C/105°C are called High heat-resistant Connector. In many cases, conventional materials are used as the base for insulators, which are commonly called "nylon connectors". Even just looking at this, the high heat resistance and temperature differ considerably depending on the type of connector.
Differences in high heat resistance depending on connector type
Our main products are connectors for board connection used in devices. The 80°C rating is usually treated as general purpose for these connectors. Connectors rated at 105°C are sometimes referred to as having high heat resistance, but due to the recent shift toward higher heat resistance requirements, our company treats 125°C compatible products as "High heat-resistant Connector." increase.
By the way, the increase in heat resistance requirements for this kind of connector is due to the increased opportunities to construct circuits in high-temperature environments such as in-vehicle parts, and the increase in heat generation due to the high performance and speed of electronic parts. Higher temperature ratings may be required in the future. In this way, the definition of high heat resistance is changing with the times and changes in peripheral equipment and component technology, even when limited to this narrow product group among connector types. In addition, various resins such as LCP, PPS, etc. are used for general-purpose grade insulation materials, such as PBT for high heat resistance. As for metal materials, alloy materials that are different from general-purpose materials are used where spring properties are particularly important, but we will discuss this later.
From here on, we will mainly talk about "connectors for board connection used in equipment", but there are many common parts for Other connectors.
High heat-resistant Connector usually refer to those with a high continuous use temperature, and the rated temperature is based on this. On the other hand, in the mounting process, etc., it may be exposed to temperatures much higher than the operating temperature for a short period of time, so I think there are many cases where heat resistance is a concern. In order to confirm both long-term and short-term durability, as an actual product evaluation, we confirm that the connector satisfies its functions and performance after the following environmental load tests.
Short-term heat resistance: Predetermined reflow conditions, etc. (180°C x 120 sec → 250°C for 2 cycles of short time x 60 sec, etc.)
Long-term heat resistance: Rated temperature (maximum allowable temperature/continuous use temperature) x specified time (125°C rating, 125°C x 1000h for in-vehicle equipment)
On the other hand, what are the general issues to be considered as a result of such environmental impacts? I summarized the rough issues of connectors for short-term heat resistance and long-term heat resistance (continuous use) by dividing them into metal parts and insulating parts.
Rough Issues to Consider Heat Resistance in Connectors
想像しやすい課題が多いのではないかと思いますが、材料部品で見た場合の耐熱に関するポイントは、概ね短期・長期とも
・熱によって溶ける・軟化する (ex.プラスチック部品の変形・溶解やメッキの溶解)
・成形/形成時のひずみが取れる (ex.金属のバネ特性の劣化やプラスチック材料の反り)
・化学反応の活性化エネルギーは温度に依存して高くなる (ex.金属の酸化やプラスチックの脆化)
の3種に集約されます。この中で、3つ目の化学反応の温度依存に関しては、その加速試験方法に関して本サイトの用語集アレニウスプロットでも少し触れていますので、興味のある方はご覧ください。ただし、この問題は先に掲げた長期耐熱の中では、現在の当社製品群の材質構成では顕在化するのが他の問題よりずっと遅いので、製品開発時の課題として挙がってくることは稀です。同じプラスチック部品を使用していても、耐熱の定義も電線等の柔軟な樹脂を動かすような製品ではこちらの課題がかなり重要なようですが(電線では寿命の定義も大きく違います)。
In addition, there are few issues related to dissolution of the plating. Therefore, from here on, while explaining Other items, let's take a look at what a High heat-resistant Connector is and what perspectives are required for development and design.
Let's start by looking at the deformation of the resin in terms of the issues faced by connectors under high temperatures. The simplest question that comes to mind is:
The problem is that if the melting point/softening point of the material is much lower than the process temperature such as reflow, it will melt. This is the minimum requirement for material selection. This corresponds to "melting/softening by heat". Another issue that lies ahead is the following, which corresponds to "removing distortion during molding/formation".
As a problem before heat resistance, it is a defect that is usually found at the prototype stage, so there may not be many opportunities for those who use connectors to see it, but deformation such as warping of resin parts before the process is introduced may have occurred. This is caused by uneven stress depending on the location of the resin that melts and flows during molding, temperature differences depending on the location of the mold used for molding, and the heat shrinkage characteristics of the resin. This issue is an extension of that. Even if the workmanship is solid, a small amount of "strain" is trapped in the resin, which is the source of such deformation. The resin tries to remember this when the temperature rises in processes such as reflow. And then I try to get back to being comfortable. For example, as shown below, when the resin tries to eliminate the distortion, it warps, and the coplanarity of the lead frame disappears, causing problems such as the legs floating off the board.
Loss of coplanarity
As I wrote earlier, these problems are affected by the bias in the molding conditions and the inherent properties of the resin. In addition to the quality of the product, for example, reflow-compatible connectors require countermeasures that consider this "remembering" part. For that purpose, it is necessary to select materials and optimize manufacturing conditions, including the flow of resin. Flow analysis by CAE is also applied, and know-how based on experience and achievements is a very important part. These are many design rules accumulated by each connector manufacturer. When it comes to manufacturing conditions, people tend to focus only on production technology, but before that, the shape of the resin part must be able to achieve the optimum manufacturing conditions. Do you feel that winning or losing is decided when you decide the shape? For example, when you take a connector in your hand, you may find that it has a recess, a taper, or an R shape that does not seem to be necessary from a functional point of view. That's it.
Strain countermeasures associated with molding
Rough contents of countermeasures against distortion associated with molding are analyzed in an easy-to-understand manner on the homepages of molding contract manufacturers, so if you are interested, please search for them.
Then, what happens in the long-term continuous use environment that causes the resin to deform? Although the temperature is much lower than the process, there are the following issues that must be considered.
As a general rule, a connector uses a spring to press metals against each other to establish a connection with a low electrical resistance value. Stress is also applied to the housing, which is also the resin part that supports the metal part, in the form of the reaction force of the spring. Therefore, if the connector is exposed to high temperatures for a long period of time while Mating, there is a risk of the following problems occurring.
As a countermeasure, the point is not only the selection of the resin, but also how stress is not applied to the structurally weak parts of the resin. For example, to put it simply, if the resin is made as thick as possible, this problem will not easily occur, but in many cases, it is not so straightforward for connector parts that have a complicated structure and are desired to be as small as possible. Therefore, one of the key points in designing a High heat-resistant Connector is how to reduce the burden on the housing and obtain the necessary contact pressure of the metal terminals in a limited space through various structural ideas. This requires ingenuity in both the spring shape and the housing shape. For example, in the structural cross-sectional view of the Board to Board Connectors below, you can see that the inner side has a structure that sandwiches the housing, and the stress on the spreading side is released by detouring the spring.
Structure example with less spring reaction force to the housing
Metal parts also have the problem of high heat resistance caused by "removing strain during molding/formation". That is metal annealing. Although this phenomenon may occur during short-term process heating, it is primarily an issue related to long-term service life under continuous use temperatures. This story is also touched on in the "What is a connector?" section of this site's Technical Info section, "High heat-resistant Connector" and "Requirements for stable connections at high temperatures." Below is the citation.
For heat resistance, maintaining contact resistance in high temperature environments is particularly important. Connector terminals, the so-called connection parts, are mainly made of copper alloy. Contact resistance depends on the contact pressure between terminals, but it is usually established by having a spring mechanism on one or both sides of a pair of connectors. Metals undergo a softening phenomenon called "annealing" at high temperatures. Originally, connector terminals maintain springiness by having a certain amount of "strain" as metal, but at high temperatures, the "strain" is removed and the springiness weakens. During this weakening process, it is necessary to achieve consistent and proper contact pressure over a given product life and within limited space and cost. The initial contact pressure should not be too strong, as too much pressure will make Mating difficult. On the other hand, maintain the necessary contact pressure even if the annealing progresses. To that end, in addition to selecting the appropriate metal material, it is important to design technology for terminal shapes that incorporate various ingenuity.
metal annealing
As explained in the quoted source, if the initial contact pressure is unnecessarily increased to maintain the contact pressure even after the metal is annealed, the Mating of the connector will become unnecessarily hard and the plating will be scraped off. It becomes For this reason, we use materials that are difficult to anneal, and devise terminal shapes that have springs that do not easily sag. In terms of materials, copper alloys such as Corson copper alloy and beryllium copper have a higher annealing temperature than phosphor bronze, which has been widely used as a spring material for connectors. is often used for high heat resistant products. There are various terminal shapes, but without exception, they have a structure that aims to be optimized in a limited space, and High heat-resistant Connector are a particular opportunity to make use of this know-how.
After overcoming the problems explained so far, our High heat-resistant Connector = 125°C rated product was established. By the way, high heat resistant products also have secondary benefits. Here's an explanation of it:
The rated temperature of the connector includes temperature rise due to energization. On the other hand, the rated current/maximum allowable current value is determined by the current value that rises by 30°C with all poles energized. Now, if the ambient temperature of the connector is 95°C, which of the 105°C rated and 125°C rated connectors with the same terminals and the same heat dissipation characteristics can pass more current?
With a 105°C rating, only a current that rises by 10°C can flow, so a connector rated at 125°C can pass a higher current value. In other words, products with high heat resistance are sometimes effective even when high currents flow.
Regarding this content, please refer to the detailed page of "Rated current" in the glossary of this site for a more detailed explanation.
Next is the last item, but let's briefly touch on cases where high heat resistance is an issue due to matching with materials other than connectors.
Among the types of connectors, there are FPC / FFC Connectors that we also handle. We also offer high heat resistance products rated at 125°C for this type, but currently Mating partners are limited to FPC. On the other hand, there are not many products yet, but some FFC manufacturers have released products that can withstand 125°C. Although we have not verified all products, we have not found an FFC that can guarantee "125°C rated connection" in combination with our products. Both are rated at 125°C, so why can't they be used as is?
First, FFC is an extension of electric wires. Recently, many companies have stopped using FFC, but in the past, most of the major electric wire manufacturers in Japan had FFC in their product lineup. It seems that the basis for the rated temperature is mainly based on UL's AWM (Appliance Wiring Material) standard for internal wiring in equipment. For these, soundness, etc., is mainly required for the bending resistance, etc. of the insulator in long-term use. The expected service life is much longer than the standard 1000 hours for automotive connectors, and in that respect it may be said that it is more stringent. On the other hand, functional requirements for Mating with connectors are not required in UL's AWM. So what happens when you actually combine it with a connector and use it at a high temperature of, say, 125°C?
In the FFC lamination process, the insulating film that serves as the base material and the conductor are attached with a thermoplastic adhesive. This thermoplastic adhesive is also present under the conductors where they make contact with the connector.
Contact point with FFC connector
When the connector is mated with the connector, local stress continues to be applied to the contact area with the Mating by the connector terminals. Since the adhesive under the conductor is thermoplastic, it will soften. As a result, creep occurs as explained in the "deformation of resin" section, and the deformation of the FFC causes the conductor to escape to the point where sound contact pressure cannot be maintained, resulting in abnormal contact resistance. Excessive application may cause loose adhesive to wrap around conductors and prevent contact.
Problems with FFC connection under high temperature
In the case of FPCs, most of the adhesives are thermosetting, so the same problem does not occur, and they can be used as they are with the connector up to the rated temperature. Connectors are required to connect FFCs, and from a connector point of view, by increasing the number of options for FFCs instead of just FPCs, a wider range of applications can be supported. This issue of FFC is not something that we, connector manufacturers, or FFC manufacturers should tackle alone, but we must work together to find a solution. As a connector, we develop FFC with higher contact pressure resistance for FFC manufacturers, such as contact points that can maintain contact pressure by following deformation of FFC and connection method development from a completely different approach. It is necessary to have We are also collaborating with several FFC manufacturers. In the near future, we may be able to unveil a product that realizes FFC connection that supports 125°C.
This time, we started with the differences in each genre of High heat-resistant Connector, and talked about some technical points. In fact, this area is a mass of know-how, and it is difficult to explain in depth on the website, so I have kept it to a superficial explanation. The technical part may have been a little lacking in content. Nevertheless, I would be very happy if you could take this opportunity to learn about various efforts to improve the heat resistance of connectors and take an interest in self-education.
こちらに当社の125℃対応 高耐熱コネクタを紹介していますので、是非ご覧ください。