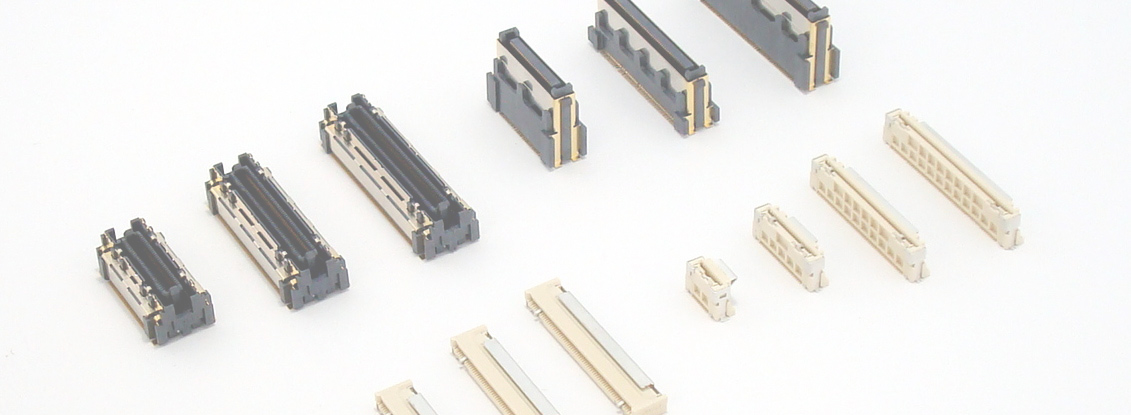
Plating is an integral part of connectors. However, the types and configurations of plating are quite complicated. I have many years of experience working as an engineer in industries other than connectors. I came to the connector industry as a non-technical person several years ago. For me, there were many things I didn't understand about connectors at first, and plating was one of them.
On the other hand, I used to deal with metals and plating in a slightly different way in my previous industry. For this reason, I thought that if I could deepen my understanding of metals and plating, it would be useful when trying to use connectors, and it would be an opportunity to acquire further knowledge, so I picked up the topic of plating this time. .
I would like to explain it as easy as possible for beginner engineers, so I would be happy if you could join me.
There is an idiom that says, "The plating peels off." Plating is thin compared to the base metal underneath, so it peels off and reveals the base material. From this, what comes to mind when you ask "what is plating?" is ornaments, especially gold plating applied to cheap metals. It's a cheaper brass plating, etc., and it's gold to give it a high-end feeling. However, tin or tin alloys (such as tin-copper) are sometimes plated in order to give a glittering effect or to hide copper, etc., which tends to discolor the underlying material. One of the purposes of plating is to provide such decoration and cosmetic support.
Plating also serves other purposes. There are three main types. The first is the decoration and cosmetics I mentioned earlier. The second is the protection of the base metal. The third is to add functionality through plating.
Keywords are shown on the right. I will explain step by step.
The third function is particularly important for connectors, but in order to understand it, it is necessary to understand the properties of the metal in the second function, protection of the underlying metal. So let's start with the second purpose, protection of the base metal.
I think 2 and 3 are fairly straightforward. In the sense that the oxide forms a film that prevents further oxidation, it seems to be generally considered as synonymous. The resistance to breakage (environmental resistance, chemicals, etc.) like this film is the resistance to corrosion. On the other hand, I think that there are many people who don't understand 1 compared to 2 and 3, so I'll move on to that.
Before we get into ionization trends, let's talk a little bit about batteries. Although somewhat simplified, Fig. 3 is an image diagram of a battery called a galvanic battery that uses dissimilar metals for the negative and positive electrodes. Each metal in the electrolyte loses electrons on the negative electrode side and is oxidized. On the other hand, the metal on the positive electrode side receives electrons and a reduction phenomenon occurs (a phenomenon in which oxygen is removed from the oxide and returns to the original metal). Current = electricity is generated by the movement of electrons at this time. By the way, in a rechargeable battery, when a voltage is applied from the "electricity extraction" point, the electrons move in the opposite direction, causing oxidation on the positive electrode side and reduction on the negative electrode side.
If dissimilar metals are brought into contact with each other and left in a high-humidity environment, a phenomenon called galvanic corrosion occurs, in which one side corrodes (for details, see dissimilar metal corrosion). is there.
What kind of metal is used on the negative electrode side? Also, if the current is determined by the flow of electrons, how is the voltage determined? This is where metals with low ionization tendencies come into play. Metals have a tendency to ionize, and have a corresponding (electrode) potential. Because it is used as a battery electrode, its potential is also called the standard electrode potential. In Fig. 4, typical metals are arranged from the left in descending order of ionization tendency.
The metal chosen for the negative electrode has a lower potential on the left, ie, a higher ionization tendency. It tends to become more ionized and give up its electrons more easily. Anode with high potential = low ionization tendency is selected. The voltage of a battery is determined by the potential difference between the positive and negative electrodes. The potential shown above is called the standard electrode potential, and the actual electrode potential changes depending on the ion concentration of the electrolyte (the relative relationship between metals does not change), etc., making things complicated. As a point here, please remember that "the higher the ionization tendency of a metal, the easier it is to let go of electrons." This means that it is easily oxidized. In the case of dissimilar metal corrosion, which was mentioned earlier, a battery is used, and electrons are taken away by a metal with a lower ionization tendency, which promotes oxidation. Even in cases where this is not the case, I think that you can have an image of "easy to ionize, easy to let go of electrons and easy to oxidize".
As can be seen from Fig. 4, gold reigns at the position where the ionization tendency is the lowest, that is, where it seems to be difficult to oxidize. Does this also match the image you have?
On the other hand, high ionization tendency = is it easy to corrode in the real environment? Does the order of ionization tendency determine the susceptibility to corrosion? This is not a simple matter, and it is a complex factor with protection by oxides, etc., and the ionization tendency is only one factor. Then, in order to protect the base metal, should we use our collective strength to plate the metal with corrosion resistance? That is of course one solution, but there are also platings with other protective functions. I will explain how plating protects bare metals, using examples of the "differences in work methods" between the two types of plating.
When it comes to corroding and rusting metals, the first thing that comes to mind for many people is probably red rusted “iron”. It may not be so common these days, but it reminds me of many rusted and fragile iron things lying around in vacant lots in the Showa era. Tinplate and galvanized iron are representative examples of plating that protects iron, which is a representative of such rust-prone metals. The iron plate is plated with tin (Sn) for tinplate and zinc (Zn) for galvanized steel.
Figure 6 summarizes their configurations and ionization tendencies. There may be some people who saw this and thought, "Huh?" Tin (Sn), which is used in tinplate, has a low ionization tendency and seems to protect iron well.
Tin, which is actually used as a plating material for tinplate, is more difficult to oxidize than iron because of its ionization tendency. In addition, the oxide acts as a protective barrier as explained in "Three Strengths Against Corrosion." Oxidation stops at that point, making it difficult to corrode. In other words, it is much more resistant to corrosion than steel, so you protect it by standing in front of it. It's just plating that feels like a guardian = guardian.
On the other hand, the zinc plating applied to galvanized steel, which has a higher ionization tendency than iron, is easily oxidized and becomes whitish when oxidized. Although it has a protective barrier function of oxide like tin, it is inferior to tin in strength against enemies. However, galvanization protects steel with another function. Fig. 7 shows the mechanism of galvanized metal protection after the plating is damaged. Suppose that the zinc has a hole in it due to the wind and rain, and water droplets enter the hole due to rain. In that part, rainwater becomes an electrolyte and a little battery-like state is formed. At this time, zinc loses electrons and begins to oxidize faster than iron rusts. The deprived electrons are sent to the iron, and a reduction phenomenon occurs at the site of the received iron (iron oxide). Zinc protects iron by rusting itself. It's like a scapegoat Jizo plating.
In addition, when the tin plate is damaged, the tin becomes the positive electrode of the battery, so the iron, which is the base metal, is damaged. On the other hand, as explained earlier, tin is a metal that is highly resistant to corrosion, so it has sufficient corrosion resistance in areas that are not damaged by external damage. Since tin is a soft metal, it can be said that the natural enemy of tinplate is trauma.
This tin plating is also used for connectors, but annealed copper wires with tin plating are also popular. Now let's compare copper and tin.
Copper wires, especially annealed annealed copper wires, are mainly used for electric wires. It's the silver wire inside the wire. High-grade, high-performance products are silver-plated (which turns black relatively quickly), and high-heat-resistant resin-coated products are nickel-plated, but you can think of them as tin-plated. is. As shown in Fig. 8, I think that there are many types that have several thin pieces twisted together.
Now the question is, why is the electric wire tinned on the copper wire? If you search why tinning is applied to copper wire, you will find that many pages say "corrosion protection". But copper doesn't really corrode. Hundreds of years old copper and copper alloy castings are well preserved. You don't hear that even unplated electric wires quickly corrode and become useless, don't they? As copper is classified as a precious metal, its ionization tendency is much lower than that of tin, and oxides prevent corrosion, which is the same for copper. Tin is much faster than copper, at least as far as the initial minor oxidation is concerned. As an engineer, I have worked much closer to electric wires than connectors, but I find it strange that the purpose of tin plating is to prevent corrosion and "protect the underlying metal."
So, the reason why people talk like that is because of the tint and how easy it is to remove. See Table 1 for a quick comparison.
copper oxide | tin oxide | |
---|---|---|
colour | Change from reddish brown to blackish brown, and then to patina (It is a superstition to say that patina is harmful to the human body.) |
transparent and discreet |
Ease of removal | Difficult to remove with stress Removable with chemicals such as acid |
More fragile than copper It is thin, harder than tin, and brittle, so it can be removed by stress. |
Why tin plating copper wire? This is because plating has the advantage of being classified as a "function" in terms of the classification mentioned in the three purposes of plating. The following two points are particularly important.
Tin-plated wire has much higher solder wettability than bare copper, so workability is improved.
Some plastics (particularly preolefin plastics) may be corroded by copper ions and their physical properties may deteriorate (called copper damage). This progresses more when it is placed under high temperature for a long time. Tin plating acts as a barrier to moderate this progression.
This has led to the discussion that plating is applied for functionality. As mentioned at the beginning, the functionality of this plating is important in connectors. Now let's move on to connector plating and functionality.
Table 2 summarizes the main metals used in connectors and their characteristics. Stainless steel, aluminum, and zinc-based metals (die-cast and alloys) are also used, but the ones listed in the table are commonly used.
metal used for plating | Metal used for base material | |||||
---|---|---|---|---|---|---|
Nickel | Tin/tin alloy (solder) |
Silver | Money | copper (tough pitch copper) |
Copper alloy | |
Used part | Base plating (also used for special contacts) |
contact plating | Base material that does not require springiness | Spring base material | ||
Conductivity (%IACS) | 25 | 15 | 108 | 73 | 100 | 10~80 |
Solder wettability | × | ◎ | ◎ | ○ | △ | △ |
Oxide film contact inhibition | Somewhat difficult to remove | Removable with a certain amount of stress | – (Do not use in environments where sulfuration occurs.) |
does not occur | difficult to remove | difficult to remove |
remarks | magnetic metal magnetic metal (Nickel Phosphorus and non-magnetic) |
Whisker generation due to stress (reduced by alloy) |
somewhat expensive
Ion Migration
(promoted by high humidity and reaction with phosphorus) Sulfurization rather than oxidation
|
does not corrode
expensive
|
inexpensive
low resistance
|
many grades |
Since we are talking about plating this time, we will be talking about nickel, tin, silver, and the king of metals, gold. Now, let's take a closer look at the functions of connector plating and these features.
In order for the connector to conduct electricity correctly, the plating of the contact part plays an important role in contacting the other side on the outermost surface. First, in order to prevent contact from being hindered, it is necessary that something that interferes with contact does not occur or adhere, or that even if it does occur, it must be reliably removed during the Mating mechanism of the connector. It is necessary to use the wiping function to reliably remove adherents and foreign matter, but since it does not depend on the type of plating, we will leave it here (please also use our 2-point contact connector, which is resistant to foreign matter).
It is the oxides and other corrosion products that we have touched on so many times that are generated as obstacles. Of the four types of plating materials, nickel, tin, silver, and gold, nickel is used for contacts of batteries, etc., because it is strong against abrasion and has moderate conductivity. Corrosion is also formed thinly, and since it is a semiconductor, it conducts. However, since it is difficult to remove by wiping, it is difficult to use in areas where low and stable contact resistance is required. In fact, none of our products currently use nickel plating for contacts.
Of the remaining three, gold does not corrode. A certain amount of contact pressure is required to remove foreign matter and adhere to the contact, but it has excellent electrical properties, so there is no blind spot as a contact material.
Silver, which is superior to gold in terms of electrical properties, actually does not oxidize easily. Some people may say, “Wait a minute, silver discolors quite a bit, doesn’t it?”, but the reason why it discolors and eventually turns black is because silver is “sulfided”, and it is in the atmosphere of sulfurous acid gas, etc. will be a problem inside. Rather than the idea of removing what is produced, it is necessary to choose not to use silver plating for connections in environments where there is such concern (if it is a little, anti-sulfurization treatment can be applied). Silver plating is much cheaper than gold and has high electrical performance, but these environmental problems and the ion migration problem described later impose restrictions on its applications.
Tin plating forms a thin, transparent oxide film on the surface. This will not grow, but it can be done relatively quickly, so the connector must be designed with an oxide layer in mind. Since the tin oxide is harder than the underlying tin, when the necessary contact pressure is applied, it cannot follow the deformation of the tin and is destroyed (like chocolate-coated ice cream when you bite into it). It is removed by wiping from there.
As a result, the contact pressure required for the connector can be roughly expressed as:
Gold ≒ Silver << Tin
The contact pressure required for silver plating should be roughly the same or slightly higher than that for gold, since there is little risk of oxidation and a sulfidation environment is avoided. On the other hand, tin plating requires a certain amount of contact pressure to remove oxides.
Now, in order to energize correctly, we must also eliminate the risk of incorrect connections. It is commonly called "short circuit failure", but in addition to being caused by foreign matter such as metal pieces, plating materials may have the characteristics that cause this risk. Tin and silver have different phenomena and mechanisms, but they carry risks.
First, when stress is applied to tin, whisker-like crystals grow. Growth is accelerated under high temperature and high humidity. It can be suppressed to some extent by alloying the plating and heat treatment. Even with connectors, we take measures such as installing insulating walls where there is a risk, but the risk cannot be reduced to zero. Therefore, tin plating is not suitable for products with a narrow inter-electrode distance or narrow pitch. Whiskers can be evaluated for reliability by observing them using a scanning electron microscope (SEM).
On the other hand, silver is known as a metal that easily migrates ions. This is a phenomenon that also occurs in batteries, etc. It is not an accurate expression, but it is a phenomenon like "reverse galvanic". From the metal of the positive electrode of a battery, rime-like crystals extend like tentacles, as if to say, "Give me quick!" the electrons emitted from the negative electrode. This phenomenon also becomes noticeable under high temperature and high humidity conditions. Phosphoric acid, etc., also contributes to this. some may be). Therefore, for silver plating, it is necessary to select an environment other than the above-mentioned sulfurous acid gas, or to avoid narrow pitches like tin plating.
You might say, "Then gold plating is fine!", but gold is extremely expensive. in terms of cost
Gold >> Silver > Tin
That's the relationship. Therefore, where possible, tin-plated and silver-plated contacts continue to be used.
Now, Table 3 summarizes the issues for correct energization, which are the contents so far.
① Secure connection | ② Do not connect to unnecessary places | cost | |
---|---|---|---|
Money | versatile | very expensive | |
Silver | Avoid sulfuric environment | Limited due to ion migration problem | somewhat expensive |
tin | Requires wiping with constant contact pressure | Limited due to whisker problem | inexpensive |
Nickel | Difficult due to strong oxide film | – | Somewhere between tin and silver |
So far, there's nothing good about nickel. But the fact that it is being used has its advantages. Let's take a closer look.
Connectors are mainly used by being mounted on the substrate by soldering. On the other hand, copper alloys, etc., which are used as base materials for connector terminals, do not adhere well to solder. It is an index called so-called "solder wettability". Plating plays an active role here as well. Since tin is the main component of solder, tin plating is very compatible with solder. Silver is one of the metals that is very compatible with solder, boasting good solderability comparable to that of tin. Gold also has very good solder wettability. It seems that if the ratio of gold in the alloy layer increases, it may become brittle, but there is no problem with the amount of gold plating that is usually applied to the soldered part of the connector. In other words, all three of the four types of plating are compatible with solder.
Nickel plating, on the other hand, is not good. It's easier to stick than stainless steel or aluminum, but it's much harder to stick than copper. You might say, "Nickel is useless again!", but that's not the case. This "solder resistance" is one of the functions of nickel plating that is necessary for connector mounting.
There is also a special nickel plating called solderable nickel plating, which is suitable for soldering, but it is not mentioned here because it is a little superfluous.
As explained earlier, both gold, silver and tin are plating materials with extremely high solder wettability. Due to its high wettability, it absorbs very well during mounting. See Figure 11. By wicking it up too tightly, there is a risk that the solder will end up in unwanted areas, such as Mating area.
On the other hand, nickel plating does not easily get wet with solder. In partial plating where gold is plated only where necessary on nickel plating (the original purpose is to reduce costs, which will be described later), solder absorption stops at the exposed nickel. In addition, even in cases where full gold plating is more suitable than partial plating for extremely small terminals, the same effect can be achieved by exposing the nickel portion using stripping solution or laser processing, in addition to masking. This kind of nickel barrier that prevents the absorption of solder is one of the plating functions brought about by nickel's "solder resistance".
By the way, gold plating is almost always nickel-plated (even silver-plated). Its purpose is to serve as a barrier, similar to the nickel barrier, but it is another feature of nickel plating that we will introduce next.
Gold and silver have the property of eroding and diffusing into copper and copper alloys. This is the case with silver plating, but it is more serious with gold plating, where thin plating called flash is becoming mainstream. The precious all-around, and extremely expensive, gold plating is getting more and more into the copper and it's going to be less. In the end, it disappears at a level that can be seen visually.
This is where nickel plating comes into play. Neither gold nor silver diffuses into nickel. Therefore, nickel plating is applied to the base material, copper or copper alloy, as a base for gold or silver plating to prevent it from disappearing. This is the second function of nickel plating.
As of April 2023, 1g of gold costs over 9,600 yen, which is an outrageous price. That's about double what it was 10 years ago. By the way, platinum, which used to be much more expensive than gold, costs just over 5,000 yen per gram, about half that of gold. Even now, according to the sales standards of the Recording Industry Association of Japan, platinum discs are ranked higher than gold discs, but in the real world it's the other way around.
Well, in terms of performance, it's all-purpose gold, but it's very expensive like this. So in the history of optimizing the cost of connectors, how to use less gold has been one of the keys.
Attach only where necessary: Selective plating
Thinning to the limit of function: thick plating → thin plating → gold flash
Selective plating is a method of minimizing the area to be gold-plated by masking, etc. after nickel-plating the substrate. Gold flash is a very thin gold plating with a thickness of 0.25 µm or less according to ASTM and in reality 0.1 µm or less. At present, this gold flash occupies a considerable weight in the plating of general-purpose connectors. Gold plating other than flash is so powerful that it can be said that it is a special specification. Even so, gold is a very wonderful metal that functions even at 1/10,000 mm or less. Expensive but...
By the way, this thin gold plating has weaknesses and countermeasures, so let's talk about them next.
As the thickness of the gold plating decreases, imperfections, specifically pinholes, increase. The amount increases and decreases exponentially with the thickness of the plating. Even though the all-purpose and invincible gold stands out and plays an active role on the surface, it is a problem if there is a pinhole. The reason why this is a problem is that galvanic corrosion occurs when it comes into contact with the foreign matter or the atmosphere that plays the role of the electrolyte, and the underlying metal is damaged. There is also a risk that corrosion products will come out and interfere with contact.
Still, gold is expensive anyway, so I want to make it as thin as possible. Therefore, a method called sealing treatment is used to fill the pinholes in the gold plating. Fig. 12 is a rough image of the sealing process, but in simple terms, the holes in the gold are filled with a liquid agent. After filling the hole, a very thin coating is formed on the surface that does not interfere with contact and prevents corrosion of the underlying metal.
Various types of sealing agents have been developed, including organic/inorganic, water-soluble/oil-based, etc., and the performance of these agents is steadily increasing. Some have the effect of improving the lubricity between contacts. Therefore, we will select a sealing agent based on usability (productivity), performance, reliability, etc. By using materials with good performance, thinner plating than before can be selected even in areas where only thick Mating and connections that require high reliability in corrosive gas. is possible in some cases.
Don't you worry about "Are the pinholes really filled properly? How do you check that?" In practice, we confirm the effectiveness of our products by verifying their reliability as products through various environmental resistance tests from the development stage. The test to check the corrosion resistant gas mentioned above is one of the tests that are easily affected by the effect and performance of the sealing treatment. There are various other tests, but the salt spray test is the one that matches the content explained here and is easy to understand from a mechanical point of view. As the name suggests, the salt spray test is a test in which the product is continuously sprayed with salt water under certain conditions. Conventionally, the purpose of the test was to confirm the resistance to corrosion caused by salt damage, but since salt water is just an electrolyte, it is forced to "battery", so it can be used for parts where galvanic corrosion due to dissimilar metals is a concern. It's perfect for washing out. If there are pinholes in the plating and the pore-sealing process is not done or is insufficient, corrosion will be confirmed in the relevant part in this test, and it can be washed out. It is also possible to conduct a combined test with accelerated corrosion conditions (actually, that is more common), and a testing machine such as that shown in Fig. 15 is used.
Ultra-thin gold plating called flash has become mainstream, but even now there are connector products with thick gold plating such as 0.38, 0.76 or 1.0 μm. In terms of performance, this is the case when the product is used in a more severe environment, or when the thickness of the gold plating is stipulated in the standards quoted for the application in the first place. On the other hand, the durability of gold flash products is also increasing, so please feel free to contact our sales staff or contact us via our website regarding the availability of specific products.
I explained "Why do you plate the terminals of connectors?" In summary, the answer to the question, "Why are connector terminals plated?" This time, we introduced the following functions.
Again, gold is a wonderful metal, but it is expensive. It's getting higher and higher. It means that there are needs in each industry, and the needs are increasing, but it is very tough. As a connector manufacturer, how to use money wisely has been a long-standing issue, and that is the point of intensifying competition. Since it is impossible to dream of a large amount of gold reserves being confirmed somewhere, our company will continue to work earnestly on this issue.