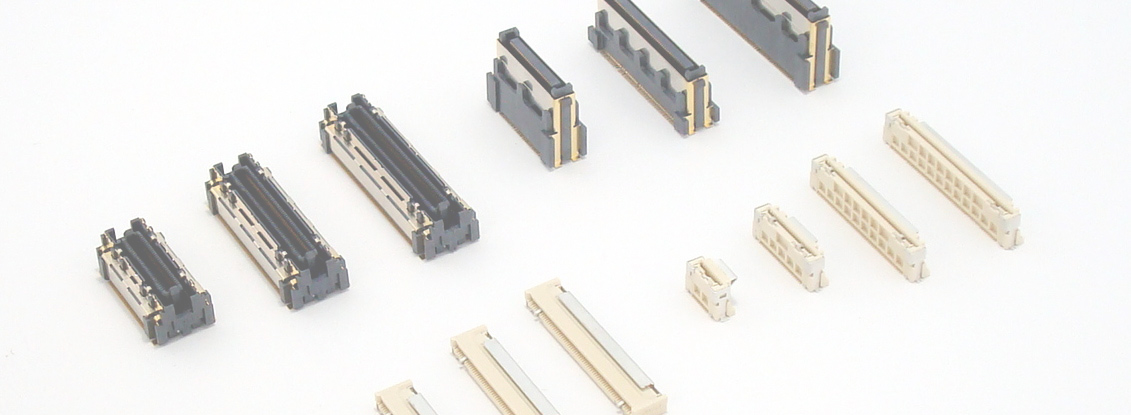
An explanation along the lines of the title is also posted on our website in the article "What is a Connector?" (We are constantly adding explanations of the origins and evolution of connectors, as well as their features, so please take a look.)
In this column, I would like to explain about the plastic and metal connectors that are used as materials, starting with some trivia about the background to their inception, which was briefly covered in the article "What is a connector?"
The static electricity that hits you in winter is followed by the rumble of thunder. There are fish that generate electricity internally, such as electric eels, electric catfish and electric rays. Electricity has been on Earth since before the birth of mankind. Humankind's wisdom has been working hard to find ways to use these incomprehensible things, or phenomena, to make them useful in our lives.
It is said that the first humans to become interested in electricity were the wise men of ancient Greece. There were probably people who found it interesting even earlier, but the first recorded instance of this was when someone noticed that amber attracted dust easily. At the time, it was confused with magnets, which were discovered around the same time, rather than static electricity. That was around BC.
From there, intellectual curiosity led to experimentation and verification, and a determination to apply it, and by the last year of the 16th century the existence of electricity was defined. In the 17th century, a device was invented to generate and store electricity through friction, and it seems that it was in the 18th century that it was discovered that lightning and static electricity are the same type of electricity. Also in the 18th century, the lightning rod was invented, and Hiraga Gennai created the Elekiteru. At the end of the 18th century, the Voltaic cell was invented, and in the 19th century, electrically powered motors, generators that generate electricity, telegraphs that send electrical signals, and light bulbs that light things were invented.
Here, there was something that was absolutely necessary in the process of establishing such technology. That was "connecting electricity", in other words, "sending and receiving electricity". Here, the invention of the electric wire, which is the predecessor of connectors, becomes important. A man named Stephen Gray conducted numerous experiments from around 1670 to 1730, and it seems that he clarified the necessity of electricity transmission by conduction and insulation. His main occupation was a dyer and an amateur scholar. Even though he achieved such great things, the less known elegance of the electric wire is the unsung hero. It is easier to see the light bulb (invented by Thomas Edison) and the motor (invented by Michael Faraday) as being "useful!", but the electric wire and connector are more modest... Of course, the light bulb and the motor are extremely important! However, the light bulb and the motor are only useful when they are connected to electricity.
As explained in "What is a Connector?", the connector is said to have been invented during World War II.
In other words, when it comes to connecting electricity, electric wires have been around for over 200 years. So, in order to understand the history of "conducting and insulating," we will start with the invention of the electric wire and explain how it led to the birth of connectors.
The basis for the electric wire first demonstrated by Stephen Gray seems to have been a damp hemp string suspended by a dry silk thread.
If you imagine it, it would look something like Figure 1.
Figure 1: Image of the first power transmission line
Figure 2 Invention of conductors and insulators
At this time, it seems that if they hung it with metal instead of dry silk thread, it became impossible to transmit electricity.
It may seem obvious if we think about it with modern knowledge, but if you hang something from a metal object, electricity will leak from that metal.
In the first place, wet hemp string conducts electricity better than wet string, so the electricity will escape.
From this, it was discovered that in order to transmit electricity, it was necessary to combine something that conducts electricity = wet hemp string = conductor, and something that does not allow electricity to escape = dry silk thread = insulator.
These things that we take for granted today were discovered only through the great efforts of our predecessors.
During the experimentation process described in the previous section, it soon became clear that metal could transmit electricity over longer distances than wet hemp string, and iron conductors were used until the mid-19th century. Due to slippage during the manufacturing process, copper was sometimes coated with copper sulfide, and it was discovered that copper performed better than iron, and copper became the mainstream conductor material from then on.
Meanwhile, insulation began with wrapping silk or paper around wires and soaking them in paraffin oil or coal tar, and rubber-coated cloth was also used. Following the invention of vulcanized rubber by Goodyear (famous for tires) in 1843, equipment for covering electric wires was also invented in 1860, and rubber-insulated electric wires appeared.
Furthermore, following the invention of celluloid in 1835, the first synthetic resin (Bakelite) was invented (1907) shortly after the turn of the 20th century, marking the beginning of the age of plastics.
The use of electric wires required the appearance of plasticized polyvinyl chloride (in 1926), a soft plastic, but plastics gradually became the mainstream insulating material for electric wires.
The copper as a conductor and the plastic as an insulator would later become the foundation of connector technology. We will explain the two materials used in connectors later, and next we will look at the technology for joining electric wires.
To connect electricity, conductors, or metals, need to come into contact with each other. There is no clear information about this technique in the early days, but people probably just glued them together, tied them together, or used brazing or soldering. The history of soldering, a technique for connecting metals, is much older than the discovery of electricity, and it is said that it was already being used to connect bronze objects around 3000 BC in Mesopotamia. It was also used to connect water pipes during the Greek and Roman eras.
In "What is a Connector?" it is stated that connectors first appeared during World War II, but if we include electrical outlets, they date back even further, to the end of the 19th century when the Edison Electric Company began supplying electricity to light bulbs in homes. They are like the predecessor of connectors, which press metal parts together even when powered to allow repeated connections. The switch, which can be considered the connector's older brother, was also developed by Edison around the same time.
It seems that the basic concept of the connector was developed in one fell swoop during the period of the invention, practical application, and widespread use of the light bulb. Even so, the way he thoroughly extracted the question, "What is needed to popularize the light bulb?" and put it into action makes us feel his incredible talent as a businessman rather than simply as a brilliant inventor.
It is said that the crimp terminal, which did not require soldering to connect electric wires, was invented around 1925, shortly before World War II.
This technology is also important as a component technology for connectors that connect electric wires. Now, at last, connectors that connect electric wires are starting to be used.
The first connectors seem to have come out in various forms at the same time, so it is difficult to identify them, but they are presumed to have been one of the cylindrical "circular connectors." The XLR connectors that are still in use today, and the N-type connectors that connect coaxial cables, were widely used for military purposes during this period.
What is important here is the utilization of copper, mentioned in the previous section, and the invention of plastic.
These materials and component technologies are important for both electric wires and connectors, but the requirements for each are different, so I will explain them in the next section.
Figure 3: Circular connectors popular during World War II
Electric wires and connectors were both invented for the purpose of connecting electricity. For connectors, which started out as a way to connect electric wires, electric wires could be considered their predecessors or creators. Another thing they have in common is that they are mainly made of plastic, which is an insulator, and copper or copper alloys, which are conductors. However, because their purposes are different, this leads to differences in the properties required of these materials. There are many differences in their purposes, but the three biggest ones would be as follows.
Overview | Electrical wire | connector |
---|---|---|
Electricity | Send far away | Broadcast on the spot |
The shape and hardness | Has the freedom and flexibility to bend | Keep it in place |
Other than the current carrying and insulation mechanism, | Nothing in particular | A mechanism for connecting is needed |
This difference leads to different requirements for the materials used.
Now, let's explain the conductors (copper and copper alloys) and insulators (plastics).
We have listed three differences in the purpose of connectors and electric wires, but let's consider how they relate to their structure and shape. First, there are differences in shape, such as size and length. Electric wires are long because they are "sent far away." On the other hand, it can be said that the size of a connector does not matter as long as it fulfills its function. (Generally, "smaller" is preferred.)
Also, for wires that are sent over long distances, you want the conductor resistance to be as low as possible. Of course, low electrical resistance is also desirable for connectors, but the priority is different for wires.
Electric wires need to be pulled in order to be "sent over long distances," and they need to have properties that allow them to be "bent." For that reason, they are basically long and cylindrical in shape so that there is no directional tendency when bent. Also, to make them easier to bend and more flexible, multiple thin cylindrical copper wires are sometimes joined together like ropes. Depending on the application, alloys, hard materials, and special materials are also used, but soft copper wire that has been thoroughly annealed is preferred because it has "no stiffness" and "high conductivity." It is a logical shape that allows it to be pulled over long distances while keeping the resistance as low as possible.
Figure 4. Example of electric wire conductor
On the other hand, perhaps the biggest difference between a connector and an electric wire is that it has a "spring" for making contact.
In principle, connectors are divided into two parts, a male and a female. In order to have a "mechanism for connecting" that involves the contact of the conductors → connection → Mating, the spring properties of the metal are used to press them together.
Also, while wires require freedom of bending without being restricted by direction, in a connector, the ability for the spring to restore its shape (or you could say maintaining its shape) and the direction in which the spring force is directed to achieve Mating are important.
For this reason, metals that have spring properties are used, even if their conductivity is somewhat lower. The conductivity of phosphor bronze, a copper alloy that is also a commonly used spring material, is about 10-15% of that of soft copper in most grades. High-performance materials such as Corson copper and beryllium copper, which have high conductivity, are also used to connect with lower resistance, but even so, their conductivity is only about 80% of that of soft copper. (If you think of it as about seven times that of phosphor bronze, it has a very high conductivity.)
In addition, the shape does not need to be long, but instead, in order to utilize the springiness for the Mating and to "utilize this function in a specific direction," it takes on a complex shape that cannot be unequivocally determined.
Figure 5 The connector conductor has a spring mechanism
Figure 6 How to make a wire conductor
With all these different shapes and materials, the manufacturing methods are naturally different as well. The conductors of the electric wires are thin and need to be made extremely long, so they are annealed while being drawn bit by bit through a die in a process called wire drawing.
The next step is to twist them together to make a stranded wire. (If you are interested, please check out the websites of electric wire manufacturers.)
On the other hand, the conductors of a connector, or parts called terminals, are mainly made by cutting and bending flat metal plates. Using a continuous processing die called a progressive die, the connector terminals with holders attached to the ends are produced at a tremendous pace.
Figure 7: Image of connector terminal processing using a progressive die
As you can see, although electric wires and connectors both connect electricity, the shapes, materials, and manufacturing methods of the conductors are becoming completely different. Although not mentioned this time, the conductors of both electric wires and connectors are plated. This is explained in detail in another article in this column, "Why are connector terminals plated?", so I hope you will take a look at that as well.
Next, I would like to talk about the differences between wires and connectors in terms of how insulators/plastics are used.
Now, regarding plastics, the important difference between them is actually similar to the discussion of metals = conductors. To put it a little differently from the previous section, it's a question of whether "plasticity" or "elasticity" is needed.
Plastics used in electrical wire insulation must be able to follow the movement of bending while also protecting the conductor mechanically and electrically. When an electrical wire is bent, a difference in "length" occurs between the inside and outside of the bend. In other words, the outside of the bend needs to stretch, as shown in the figure on the right.
Therefore, the insulating material used for electric wires must be stretchable. If it does not stretch enough, it will not be able to bend, or the insulation will crack or break if it is forcibly bent. One reason plastic is used as an insulating material for electric wires is because of the plasticity that plastics have, and materials with particularly high plasticity are selected for use. Alternatively, materials that are originally hard, such as polyvinyl chloride, are mixed with a material called a plasticizer before being used as an insulating material.
Figure 8 When an electric wire is bent...
This softness is the most important factor in determining deterioration and life expectancy. Of course, there are other factors such as insulation performance and strength, but the "softness that does not break when bent" is important because it can easily be lost through deterioration. I'm sure some of you have seen electric wires that have become so hard that they snap when bent.
On the other hand, connectors must maintain their shape precisely in order to function as Mating connector. Naturally, materials with a certain degree of hardness must be used. The guidelines for deterioration and life span are similar, and it is important to maintain the shape. Not only long-term use, but also short-term heat resistance, such as the soldering mounting process, is important. For wires, short-term heat resistance that is compatible with soldering brings convenience, so high-melting point materials and cross-linking (complicating the molecular bonds of plastic to make it less likely to melt) are sometimes used, but this is only to prevent the material from melting and flowing or shrinking excessively. Regarding the shape maintenance of resins used in connectors, especially at high temperatures, we have also touched on this in another article in the column, "What is High heat-resistant Connector?", so please refer to that as well.
Now, we mentioned that it is necessary to use a material that is relatively hard in order to maintain the shape, but there are also cases where the bending elasticity of resin is required.
For example, when adding a mechanism that creates a clicking sensation or sound when Mating, the convex part first rides up onto the other part as shown in the figure, and the resin advances in a momentary warped state, and when it reaches the specified position, it slams into the concave part with a "snap" sound so that it fits into place. Also, after Mating, it needs to return to its original shape exactly.
In other words, what is required of plastics is not the ability to remain in place when bent, but the ability to return to its original shape = spring-like elasticity.
Figure 9. Image of Mating with clicking sensation and sound
There are many other cases where plastics are required to have spring elasticity in connectors, such as locks and part fixing mechanisms. The differences with electric wires are similar to those with conductors. Because of these differences, the manufacturing methods and materials used are naturally different.
To insulate long electric wires, a process called "extrusion molding" is used.
The molten resin is placed over the conductor using a device called a crosshead, and squeezed out through a die with an appropriately sized hole. This is pulled at a speed that matches the amount of resin applied with the desired thickness of the wire, and then cooled in a water tank to create a long wire. On the other hand, most resin parts for connectors are manufactured using a method called "injection molding" (though in rare cases they are made using other methods such as cutting).
Resin is poured into a mold that has a "negative" shape of the required shape, cooled and hardened, and then removed, and the unnecessary parts that form in the resin path, called runners, are cut off (similar to how plastic models are made) to finish the part.
This is a molding method that is suitable for both long wires with simple shapes and small connectors with slightly complex shapes.
Figure 10 Extrusion and injection molding
The materials used for wires and connectors also differ.
When it comes to electric wires, the mainstream are broadly divided into PVC-based, polyolefin-based, and fluororesin-based. There are also various other types such as various urethane-based and nylon / polyamide-based types, but I think the three categories mentioned above are the mainstream. A distinctive feature is that, apart from fluororesin, materials mixed with various recipes are used. The materials used are not limited to petrochemical resin-based materials, but also include metal-based (metal oxides, hydroxides, etc.) and mineral-based materials. It is also not uncommon for each electric wire manufacturer to develop insulating materials with their own unique mixtures, and most large companies in particular do so.
In addition to nylon, which has a long history, connectors often use so-called engineering plastics (engineering plastics) and super engineering plastics that are suitable for connectors. Apart from nylon-based materials, the three main types used are PBT, LCP, and PPS (nylon-based materials are also classified as engineering plastics/super engineering plastics depending on the grade).
We use all types, but the proportion of LCP is increasing recently due to the increase in reflow compatible connectors. Plastics for these connectors are sold in various grades by each resin manufacturer. In fact, I have never heard of a connector manufacturer independently developing or compounding materials like the materials for electric wires. It is just my impression, but compared to electric wire manufacturers, connector manufacturers may be more specialized in "establishing production technology that can be used well," and may select materials not only for performance but also for ease of manufacturing parts and stability. It is strange that even if the exact same grade of material is used, the quality and dimensional accuracy of the finished product vary greatly depending on the manufacturer.
Figure 11 Comparison of plastic materials used in wires and connectors
For more information on the characteristics of each material, please refer to the websites of the material manufacturers, so we will not explain them here (although we may do so on another occasion).
This time, I started by talking about the birth of the act of connecting electricity, and then gave a simple explanation of the trends regarding the conductors (metals) and insulators (plastics) used in connectors, using electric wires, which are the predecessors in this field, as a comparison.
This time I've only touched on the ingredients, so I may have another opportunity to explain them in more detail.
Or, if there are people who have read this column and become intrigued and are now researching various materials, I would be very happy. Let's live each day with curiosity.